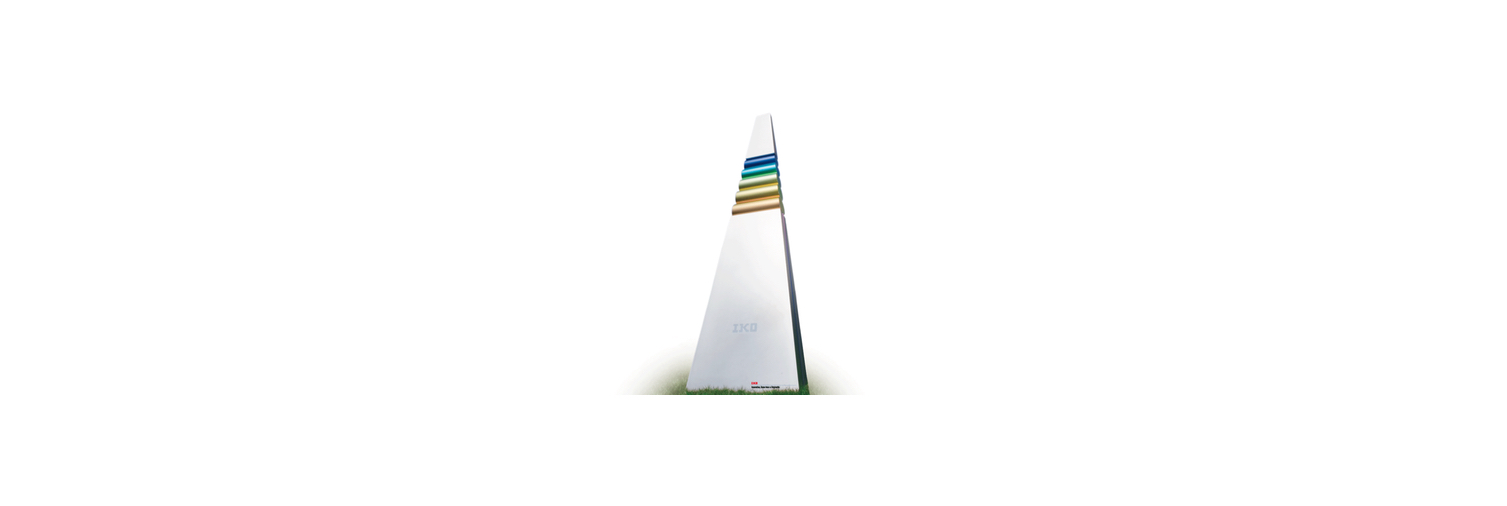
IKOエピソードNo4 EPISODE-004 開発担当者インタビュー
「技術の品質」を追求し、社会に貢献する新たな価値を創造
IKOは、ニードルベアリングの自社開発を国内で初めて成功させています。このような高度な技術開発力は、高い品質や柔軟な顧客対応力と並ぶIKOブランドの大きな強みです。既存品とはまったく異なる形で、直動案内機器のメンテナンスフリーを実現した「Cルーブ」も、そうした高い技術力が生み出した製品の一つ。「技術の品質」にこだわりながら、真摯な姿勢で次世代の軸となるようなイノベーションを生み出す技術研究所の開発担当者にお話を聞きました。
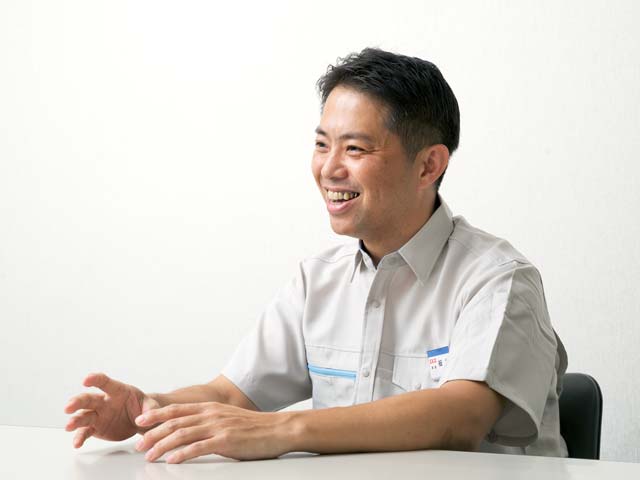
あらゆる場面で社会を支えるベアリングの技術開発へ
入社の経緯と、当時の担当業務について教えてください。
日本トムソンという会社とIKOというブランドを知ったのは、機械工学系の大学院生として就職活動をしていた時のことでした。人を大切にする会社で、技術もしっかりしていると、研究室の先生が勧めてくれたんです。ベアリングという部品が医療機器や産業用機器など社会のあらゆる場面で使われていることも知り、社風なども見て「さまざまなことに挑戦できそうだ」と考えて就職を決めました。
入社後は、新技術の開発や製品の信頼性評価などを行う部署に配属され、まず製品の耐久試験などを担当。その後、当時業界で注目を集めていた直動案内機器のメンテナンスフリー化にかかわることになりました。
“直動案内機器のメンテナンスフリー”について詳しく教えてください。
直線のレールの上をスライドユニットが移動する直動案内機器は、例えば半導体製造装置や医療機関のCTスキャンなどに活用されています。通常、これらの機器をスムースに動かすには、外部から定期的に潤滑油を供給する作業が必要ですが、私が入社した頃には、スライドユニットに潤滑部品を外付けすることでこの作業を自動で行う他社製のメンテナンスフリー製品が世に出回り始めていました。
直動案内機器で高い評価をいただいていたIKOが、この分野で遅れを取るわけにはいきません。そこで上司に助言をもらいながら、研究所のメンバーと知恵を出し合って試行錯誤を重ね、「ごく小さな穴が連続して並ぶ連通多孔質状に成形した樹脂に多量の油を含ませる」という独自技術を開発。「Cプレート」という名で販売を開始しましたが、開発はそれだけでは終わらなかったのです。
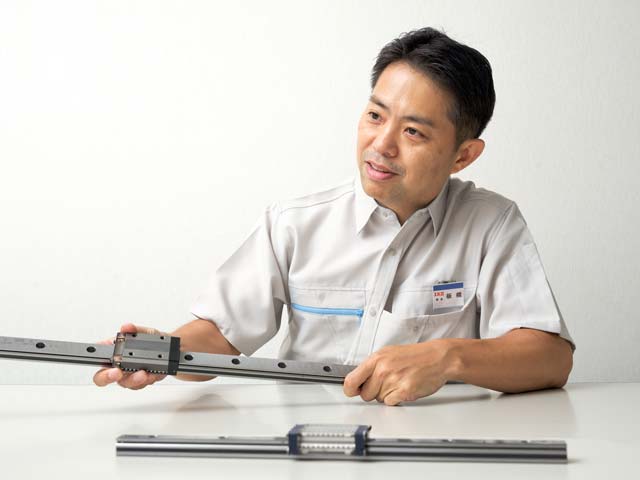
前例のない製品「Cルーブ」の開発は難航を極める
IKO独自のメンテナンスフリーを実現した後も、なぜ開発が継続されたのでしょうか?
「Cプレート」は、仕組みはオリジナルでしたが、“スライドユニットに外付けする”という点は他社製品と同じでした。ただこの方法には、潤滑部品の分だけスライドユニットが長くなってしまい、その分レールも延長する必要が出てくるというウィークポイントがありました。もし仮に潤滑部品をスライド部に内蔵できれば、このような課題を解決することができると同時に、既存品との置き換えも容易になります。そこで、スライドユニットに潤滑部品を組み込むという、これまでにないメンテナンスフリー製品の開発計画が持ち上がったのです。
現在もIKOの主力製品である「Cルーブ」につながるわけですね。そこから製品化まではどのようなプロセスをたどったのでしょうか?
潤滑部品である樹脂は、スライドユニット内の一部となるわけですから、そこに不具合が生じた場合は製品自体が成り立たなくなってしまいます。ですから耐久性は「何をやっても大丈夫」と言えるくらいまで確認する必要がありました。そこで、耐久試験機を増設し試作と評価を繰り返しました。
こうしてようやくIKOの名にふさわしい品質を実現し、会社も発売に向けて動き出していたあるとき、重大な問題が表面化しました。超高速で数カ月に及ぶ連続運転試験をかけていた試作品の一部に不具合が生じていたのです。ボールタイプの転動体がユニット内を循環する際、部品が破損していました。
この問題に気づいたときは、頭を抱えました。しかし、ごく特殊な使用環境を想定したテストの結果とはいえ、不具合が起こりうる製品を世には出せません。相談した上司も私と同様の意見で、発売の延期を即断。設計部門とも対策のディスカッションを重ね、当初は従来品と共用にしようと考えていた樹脂部品の構造をゼロから見直しました。
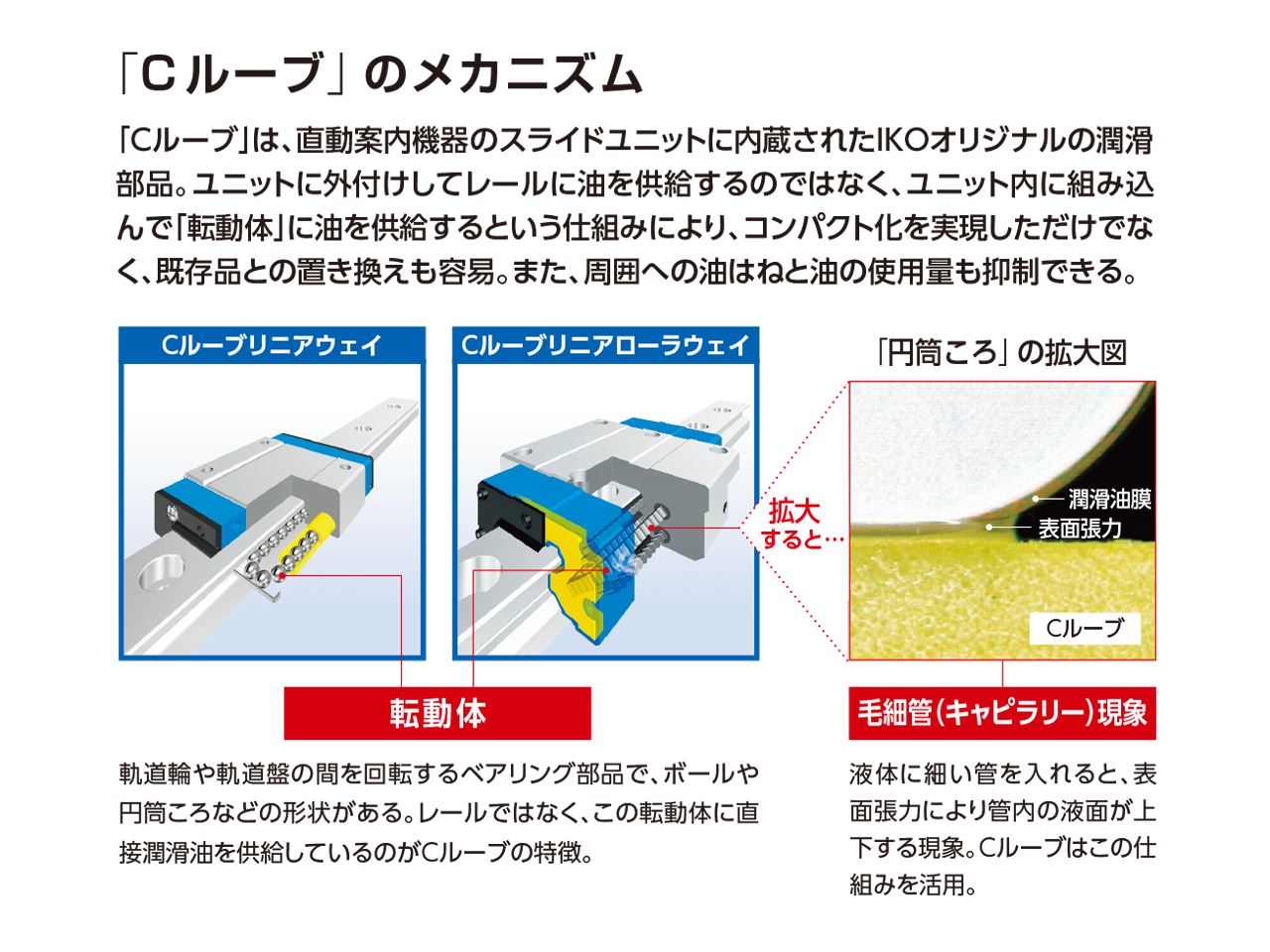
“オールトムソン”で新たな価値を持つIKO製品を完成させる
チームを挙げて、再び試行錯誤の毎日が始まったわけですね。
結局、これで大丈夫という製品を完成させるにはそれから1年と少しの時間がかかりました。従来品と別の仕組みを構築するとなると、生産では新しい型が必要になり、販売時の在庫も多く持つ必要が出てくるため、経営層にとっても大きな決断だったはずです。しかしその結果、お客様に自信を持って提供できる、長期メンテナンスフリーを実現する「Cルーブ」が完成しました。販売開始から20年近くが経過していますが、これまでに潤滑トラブルは1件も出ていません。
「Cルーブ」は、他社製品のようにレールではなく、製品内部の転動体に必要なだけ潤滑油を供給するシステムになっているため、周囲への油はねも少なく、油の使用量も抑えられ、外付けだと避けられないレールへの摩擦もありません。また、コンパクトで既存品との置き換えも容易な上、自立した樹脂に潤滑油を含ませる仕組みであるため、要望に合わせて油の種類をカスタマイズすることも可能。クリーンルームや低温・高温環境、真空中など、特殊環境に求められる仕様にも対応できます。実際、「Cルーブ」が組み込まれた直動案内機器「Cルーブリニアウェイ」は、半導体設備をはじめ、医療用機器、食品や薬品の製造機器、分析器など、要求が高度化する傾向のあるさまざまな分野で活用いただいています。
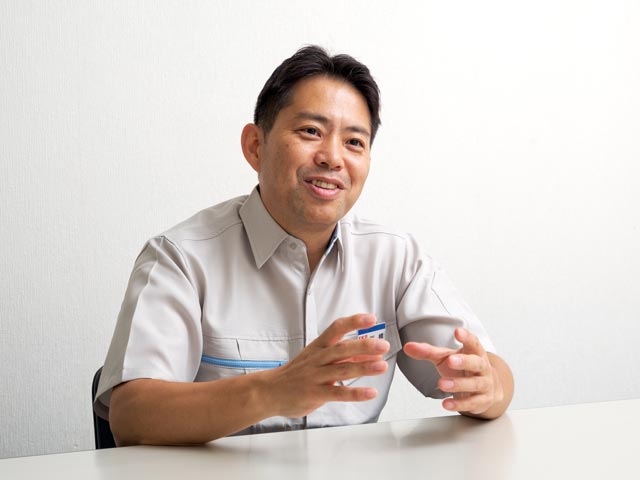
「Cルーブ」のように、画期的で長く社会に必要とされる製品をIKOが開発できたのはなぜだとお考えですか?
樹脂が削れるという問題が明らかになったとき、当時の上司はそこをうやむやにしたり、開発を終わりにしたりしようとはせず、社内のあらゆる関係部署を動かしながら、より強力に技術開発を追求できる環境を作り出してくれました。他部署の協力を得ながら、オールトムソンで新たな価値をもつ製品の開発に真っ直ぐ向かっていく。そんな上司の姿勢を目の当たりにしたとき、社会の軸を支えるIKOブランドの技術担当者であることに対して改めて誇りを感じるとともに、技術開発の面白さも再認識しました。
私はその後、岐阜の開発センターで既存製品のナノレベルの超高精度仕様の開発などに2年ほど携わり、現在は再びCルーブを生み出した鎌倉の技術研究所に戻って研究チームを統括しています。私もチーム全体、さらには生産や販売など社内の他部門のニーズに目を配り、その課題解決に協力しながら、IKOの技術開発力をさらに高められるような環境づくりを心がけています。
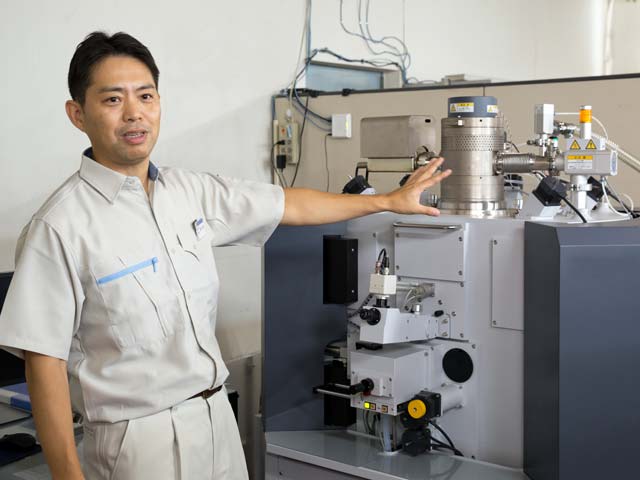
IKOのブランド理念のもと、社会に貢献する技術を生み出したい
研究面では、現在、どのようなことに取り組まれていますか。
現在は、社内だけでなく産学連携を含めたオープンイノベーションでさまざまな研究を進めており、これまでの世に出ていないような革新的な技術開発を引き続き推進しています。
世にない技術をゼロから研究するなかでは、失敗することも不安を感じることも多々あります。ただ、抱えている課題について考え続けていると、「これだ」というアイデアが降りてくる瞬間がある。そうして上手くいった時の喜びはひとしおです。何よりその技術が製品という形になって世に出て、社会の軸を作り上げ、お客様にも喜んでもらえます。こうしたことが一番のモチベーションになっています。
今後、IKOで実現していきたいことはありますか。
「社会に貢献する技術開発型企業」を経営理念に掲げる日本トムソン、IKOブランドの技術担当者としてよく考えるのは、「技術の品質」の重要性です。仮に開発中の技術がお客様の不利益になるものがあったとしたら、隠すことなく正直に真っ直ぐな対応で向き合い、後に信頼してもらえるような技術にする。そうした行動の積み重ねが、IKOブランドの今を作っていると考えています。
今後もIKOブランドの理念である「Innovation(革新)」「Know-how(ノウハウ)」「Originality(独創性)」に恥じない形で研究を進め、新たな技術を生かした独自の使いやすい製品づくりを通して、地球環境やよりよい社会づくりに貢献していければ嬉しいですね。