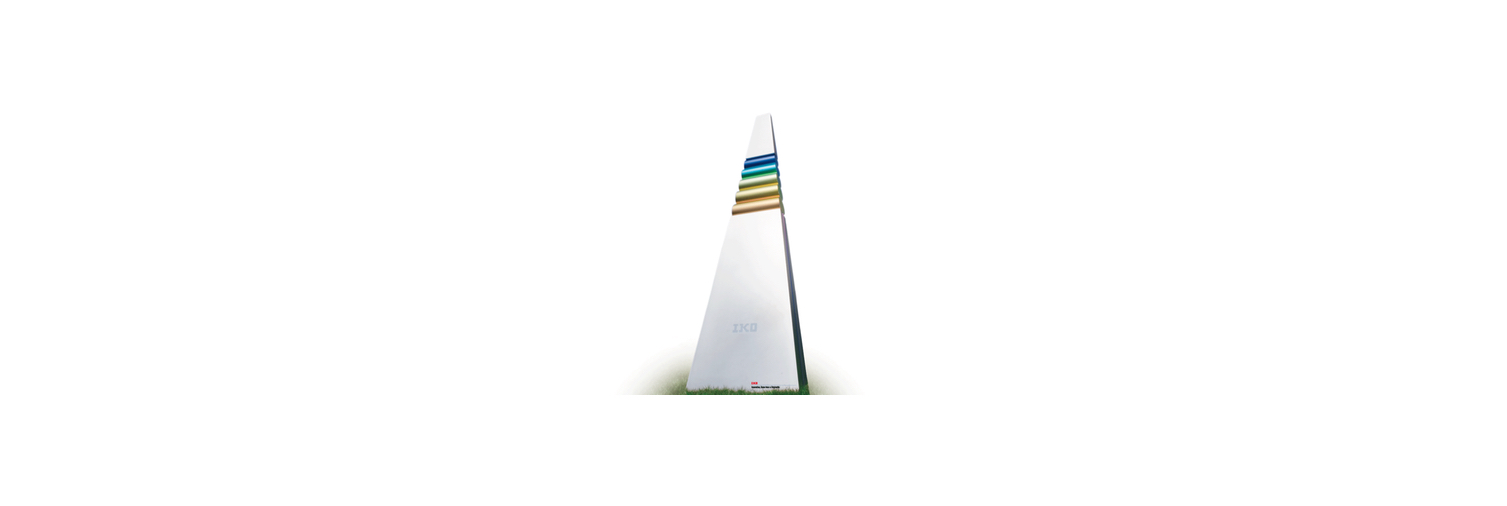
IKOエピソード EPISODE-001 品質管理担当者インタビュー
IKOらしい真っ直ぐな思いで“IKO品質”を実現する
IKOブランドの最大の強みは、丁寧に作り込んだ“品質”──。その強みを実現しているのは、あらゆる関係者たちの「IKO品質をさらに向上させたい」という真っ直ぐな思いです。IKO製品の製造工程を担当した後、現在は各製品の最終的なクオリティをチェックする部署で人材育成に尽力するなど、IKO品質を長年支えてきた検査部門の方に話を聞きました。
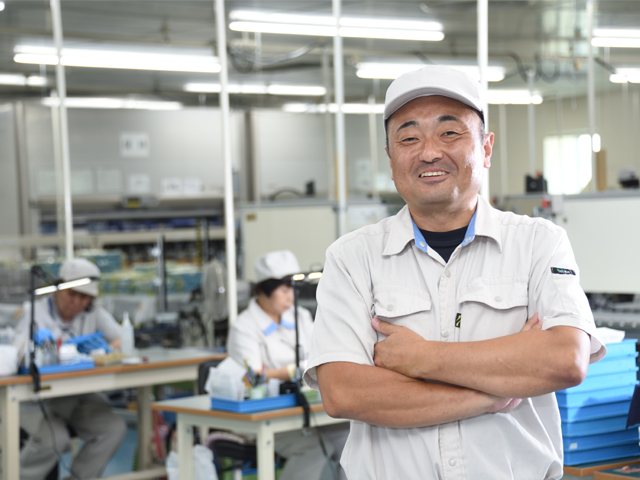
~焼入れ・焼戻し~
焼入れの工程 高温で加熱し硬度を上げる
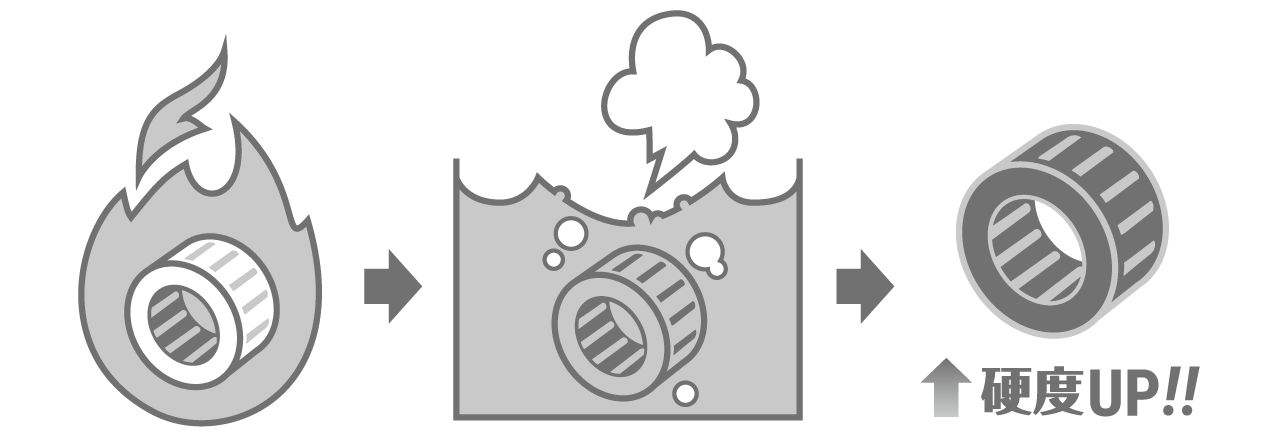
焼戻しの工程 低温で加熱し靭性を高める
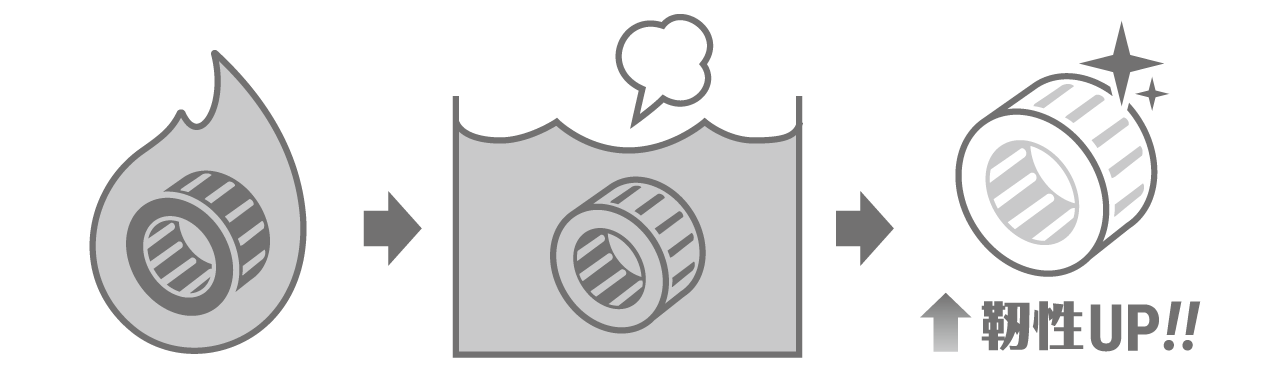
ベアリングの製造工程には、2回の熱処理工程があります。1回目は「焼入れ」といい、高温で加熱し冷却することで金属の硬度を上げます。しかしこのままでは非常に硬く、割れが生じやすい状態になっており、長時間の使用に耐えなければいけないベアリングには使用できません。そのため2回目の「焼戻し」を行い、焼入れよりも低温で加熱し冷却することによって靭性(じんせい)を高め、ベアリングに耐久性を持たせます。
チャンスを与えてくれる土壌の中で職人技を極める
これまでどのような業務を担当されてきたのか教えてください
機械科の高校を出ていた私は、当時からおぼろげながら「将来はモノづくりをしたい」と考えていました。入社後はそんな私の希望通り製造工程のさまざまな業務を担当しました。いずれも印象深い業務でしたが、その中の一つに「熱処理工程」がありました。
ベアリングの製造では基本的に金属をそのまま使うことはできず、加熱・冷却することで組織構造を変化させ、硬度などの性能を向上させる必要があります。その工程は熱処理と呼ばれ、熱の入れ具合は現場の担当者によって調整されます。熱の加え方や冷却の方法で製品の強度や寿命が変わってくるので、熱処理工程はIKO品質を保つ上でかなり重要なプロセスと言えるでしょう。
製造機器と向き合うなかで、“IKO品質”の高さを実感
入社当時から長期間、IKO製品の製造に情熱を注いできたわけですね。
入社してしばらくは製造工程での勤務が続きましたが、後に「生産設備部門」への異動も経験しました。ここでの業務は、IKO製品を作る生産設備の保全・管理です。それまで入社から長い間、IKOの「製品」そのものと向き合ってきたわけですが、ここで初めて製品を生み出す「機械」と向き合うことになりました。
IKOの品質の高さをダイレクトに実感したのが、この業務を担当している時でした。IKO製品は高品質と言われていますが、他社製品に携わる機会は当然なく、比較ができなかったため、IKO品質を実感する機会が乏しかったのです。しかし、実際に機械と対峙してみると、組込まれている部品にIKO製品が使われているものは明らかに不具合が生じるケースが少なく、部品としての寿命も長い。最新鋭の機械を、自分たちが作ったIKO製品が支えていることを誇らしく感じました。
それからまた製造工程に戻るのですが、その時は管理職となっていました。「製品」「機械」と来て、今度は主に「人」と向き合うようになりました。この状況は現在の検査部門でも続いています。
最先端技術と熟練の技が“IKO品質”を支える
現在の検査部門の業務はどのようなものでしょうか?
簡単に言うと、各製造工程を経てきた製品がいよいよ出荷されるという直前の段階で、それが本当にIKO製品として社会に届けていい品質になっているかどうかを最終チェックする関所になります。 検査では工程仕様書や図面と照らし合わせて指示通りの仕様になっているかを確認するほか、熟練スタッフによるチェックなども行います。IKO製品の品質は、最先端の技術とスタッフの熟練の技が融合して生み出されている、そんなふうに言えると思います。
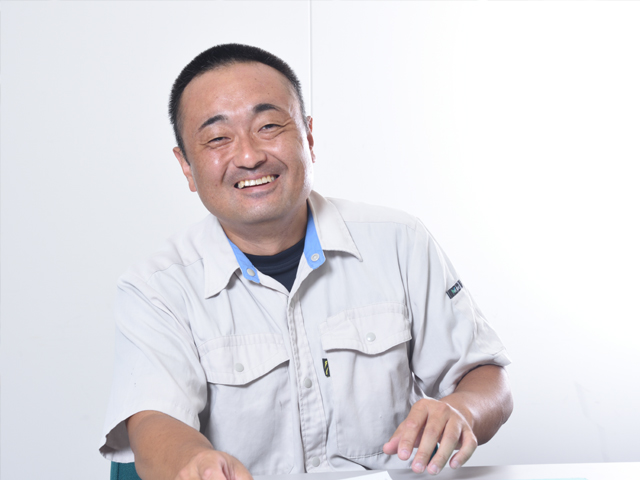
IKO品質を実現する人材を育てるために
チームをまとめるリーダーとして気をつけていることは?
担当する工場の検査部門には約50名のスタッフがいます。その全員に毎日必ずあいさつし、積極的に声を掛けるといったことはもちろんですが、ほかにチームをまとめる上で気をつけていることが3つあります。
1つ目は、「すべての情報をチーム全体で共有する」こと。
2つ目は、「やりたいことに積極的にチャレンジできる土壌を用意する」こと。
3つ目が、「単に“言う”のではなく、しっかり“伝える”」という意識です。
私は仕事で一番難しいのは、“人づくり”だと考えています。IKO製品の品質は、その高品質を実現できる人たちによって作られている。そこで、いかにしてIKO品質を未来につなぐ人材を育成し、自分自身も共に成長し続けていくかが大切になります。その方法を考え、実現していくことが、これからの私の役割ではないかと感じています。
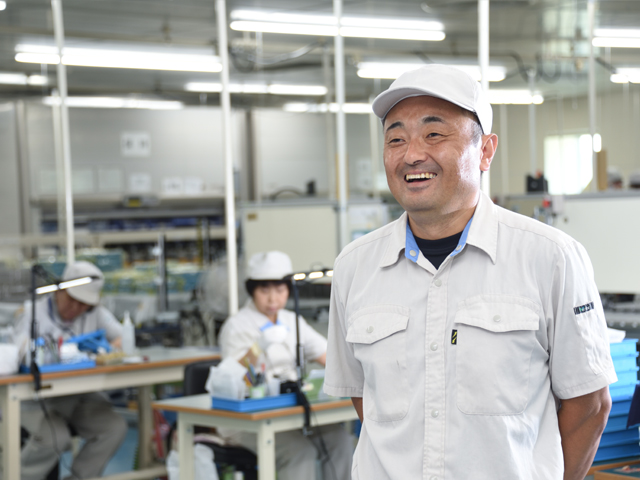
製造担当者たちに共通するのは、品質への強い誇り
IKOの最大の強みである“品質”を管理するプレッシャーはありませんか?
検査という業務には重い責任が伴いますが、実はプレッシャーというものはそれほど感じていません。なぜなら私が知る限り、IKO製品を生み出す各製造工程の担当者で、品質に対する意識が低い人は一人もいないからです。みんな品質を良くすることに強い誇りを感じていて、「これでどうだ」というものを真っ直ぐな思いで作り込んでから、次の工程に回していく。私はさまざまな現場を経験し、そのことを身をもって実感してきました。検査には、そうして各工程で真剣に作り込まれたものが回ってくる。いい加減な製品が送り込まれてくるわけがないのです。
ただ、最終品質をチェックするというのはやはり責任重大ですから、スタッフは常に「この検査の仕事ぶり一つで会社を潰すこともある」ということを意識しています。IKOにとって品質は第一です。品質を維持するために、時間をかけてでもやることはきっちりやる。それこそがIKOであり、“IKO品質”を実現する上で欠かせない鍵であると私は考えています。